In the realm of waste containment, geomembrane is used extensively to prevent leakage and protect the environment. Motors play a crucial role in powering the equipment necessary for installing, positioning, and maintaining these systems. This article explains the importance of various motors, particularly electric and hydraulic, in geomembrane projects.
What is a geomembrane?
A geomembrane is a synthetic membrane used for containment purposes in landfills, wastewater treatment plants, and other environmental applications. It is designed to resist permeation by liquids and gases, preventing contamination and environmental damage.
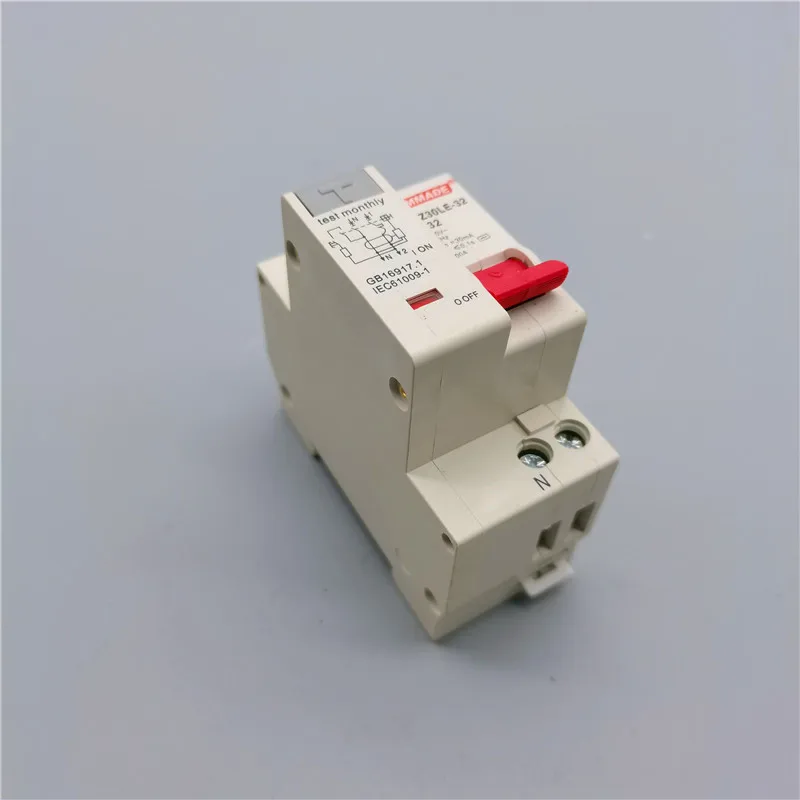
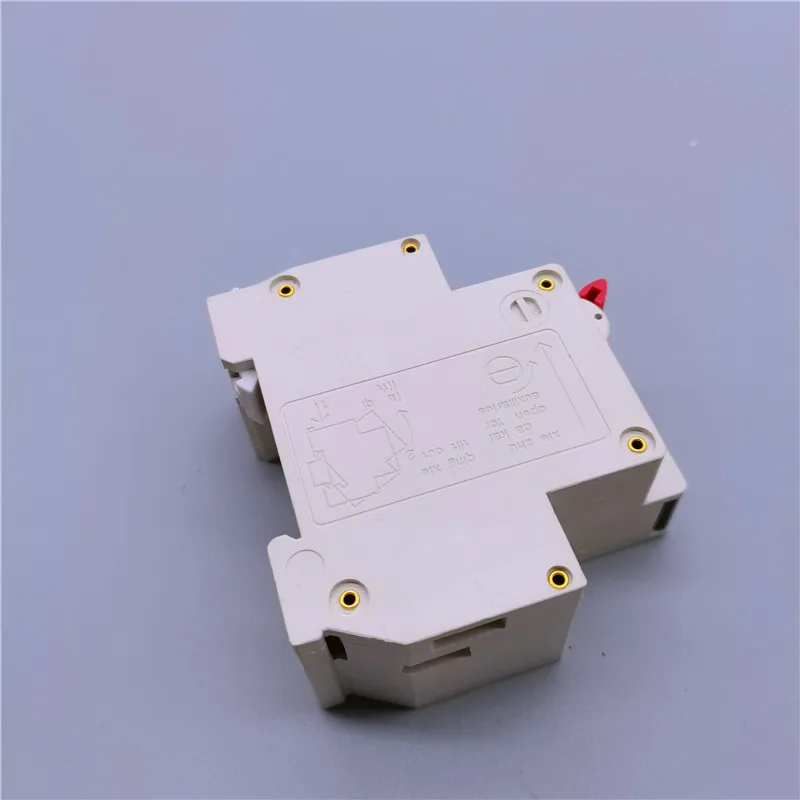
How do motors contribute to geomembrane installation?
Motors power the machinery that transports and installs geomembrane liners, from heavy-duty cranes and rollers to automated cutting machines. These motors ensure the material is positioned and sealed without wrinkling, tearing, or misalignment, which could compromise the containment system.
What types of motors are commonly used in geomembrane applications?
- Hydraulic Motors: Used for heavy lifting and moving large rolls of geomembrane in tough environments.
- Electric Motors: These provide precise control in equipment used for cutting, welding, and positioning geomembrane.
- Pneumatic Motors: Often used for smaller tasks where a clean, compact motor is needed for precise control.
How do motors ensure the longevity of geomembrane systems?
By powering equipment that ensures proper installation, motors help maintain the integrity of the geomembrane during deployment. Proper installation is critical to avoiding defects that could lead to leaks, ensuring that the containment system lasts for years with minimal maintenance.
Motors are vital in geomembrane applications, ensuring efficient, precise installation and maintenance of waste containment systems. Whether electric, hydraulic, or pneumatic, motors support the durability and reliability of these essential materials.